I’ve had my MakerGear MK3-ID for a year or so now, along with a Prusa MK3S. The Prusa MK3S with it’s removable flexible build plate is my ‘go to’ printer for almost everything that can be done with a single extruder. The flexible build plate is wonderful – it makes printing so much easier. Fortunately there is now a comparable option for the MakerGear M3-ID – BuildTak’s 8×10 FlexPlate System. I was able to find the correct size system for my M3-IE at Partsbuilt 3D and it arrived in just a few days (unfortunately with Ohio state tax applied as both the company and I are in the same state). This system makes a HUGE improvement in the ease of printing with the M3-ID, and consequently make it a much more appealing alternative to printing everything on my Prusa. Here’s a photo of the FlexPlate base on my M3-ID.
However, there were a few ‘gotcha’s’ during the installation, necessitating some modifications to the M3-ID.
- The stock M3-ID comes with a 4mm glass build plate, mounted on top of the heating element, and held down with screw-down rotating clamps at each corner . There’s no need to keep the glass build plate with the BuildTak FlexPlate system, but the resulting 4mm gap means that the stock clamps will no longer hold the build plate down firmly (or at all, for that matter).
- The FlexPlate system consists of a mounting plate with a number of embedded magnets that is affixed to the flat heating plate with an adhesive film, and a flexible steel build plate onto which the actual build surface (either a BuildTak or PEI sheet) is adhered. The steel build plate attaches magnetically to the mounting plate, and can be easily removed and flexed to pop the print off, a la the Prusa MKS system. However, it turns out that while the mounting plate with embedded magnets mounts quite nicely on the heated base, the 8×10″ steel build plate is just a smidge too large in both dimensions for easy mounting/dismounting. It tends to overhang in one or both dimensions, meaning that one corner rests atop its corner hold-down block, and then the plate isn’t quite flat. This problem could easily be fixed if the steel build plate was just a few millimeters smaller in both dimensions.
- The Prusa MK3S has a simple and elegant way of achieving excellent physical registration of the flexible build plate when it is placed onto the printer. There are two small protruding posts (3 or 4mm screws, actually) at the rear of the print area, and the flexible plate is notched so that when it is placed against the screws, it lines up perfectly every time. There is no such physical registration feature on the M3-ID, so getting the plate down correctly so it isn’t overlapping one of the corner pieces is a bit of a PITA
So, I needed to make a couple of modifications to the M3-ID corner hold-down system. The idea was to make the build plate fit without binding, and to achieve better physical registration of the build plate when it is re-installed onto the M3-ID after popping off a print.
The first thing I did was simply place a couple of 3mm hex nuts under the hold-down clamp foot at each corner, filling the gap left by the 4mm glass build plate, as shown below.
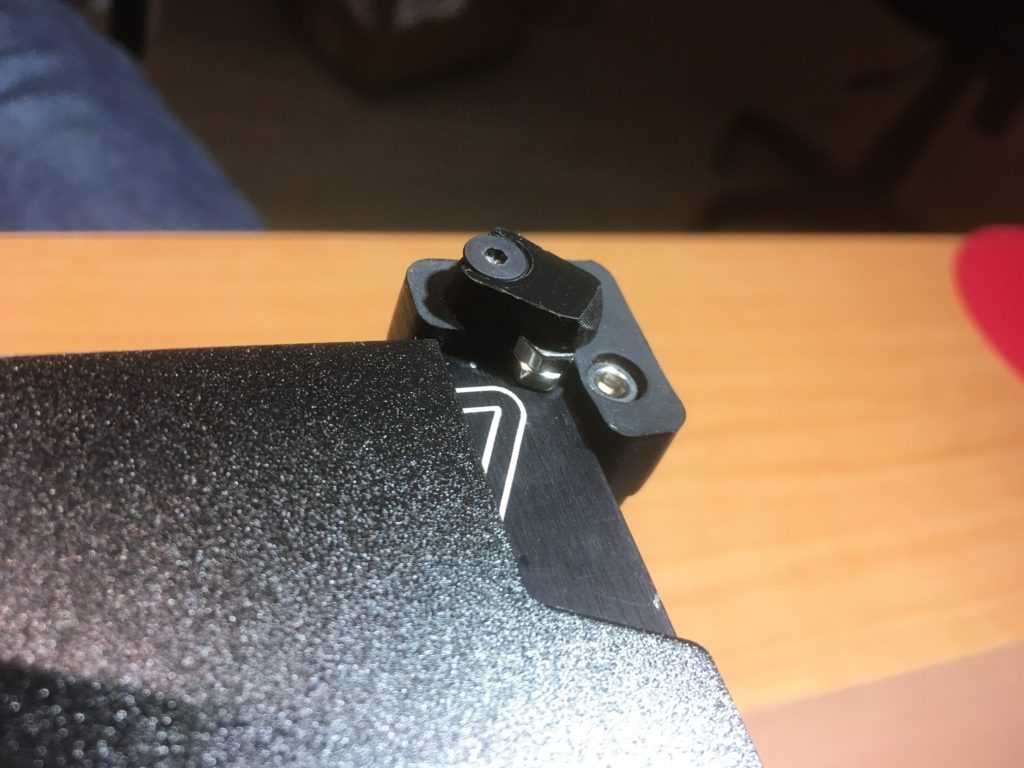
This worked – sorta – but it wasn’t very elegant and didn’t address the other issues, i.e. the flex plate interference, and the problem of physical registration. So, I started designing some alternate hold-down clamp and corner pieces to do a better job. The first effort was a modifed hold-down clamp, as shown below:
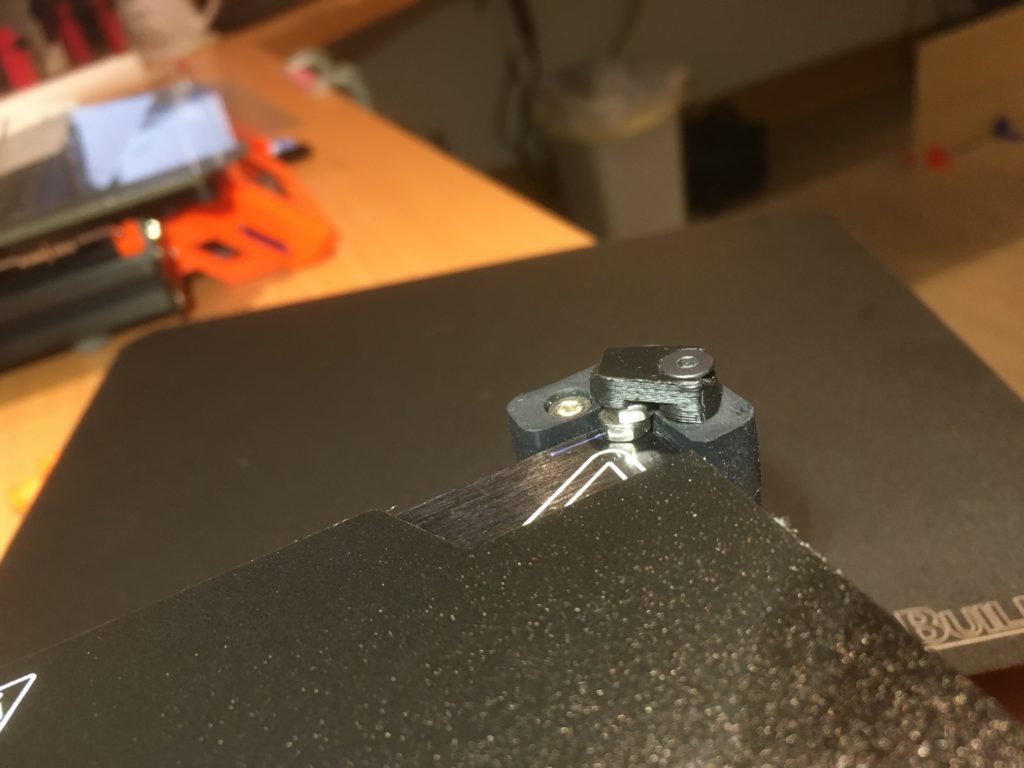
The thing I love about 3D printing is that you can iterate through several designs rapidly and learning from each version. I usually go through half a dozen versions before getting where I want to go, but it is so cheap and fast that doing it this way is MUCH faster than trying to do a ‘moon-shot’ on-off solution (which generally doesn’t work anyway, due to some unknown unknown).
So, back to the drawing board (TinkerCad) and some more designs. I started with designs to replace the stock corner blocks, and after six revs, had the following final design
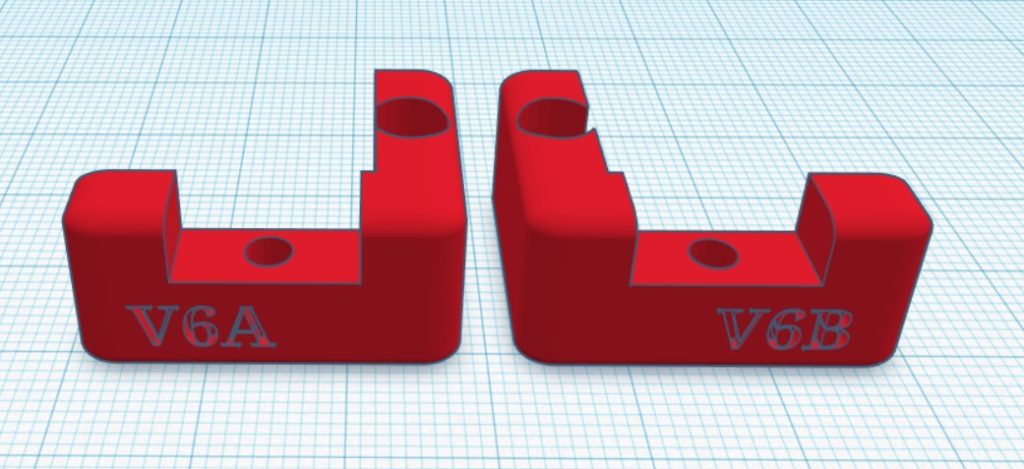
and the final design for the hold-down clamp:
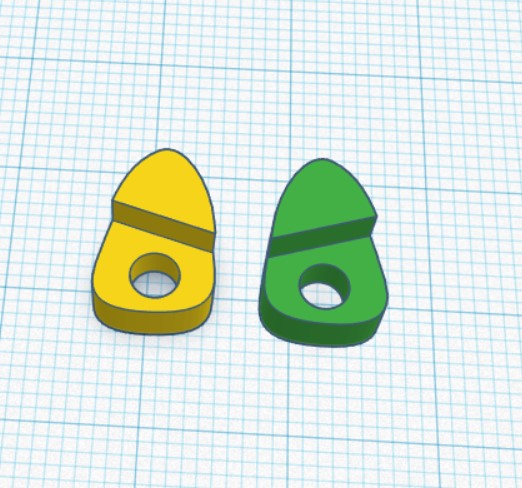
Both the corner blocks and hold-down clamps were printed with left/right mirror images to match the mirror-image corner requirement.
After getting all the final versions printed up, I installed everything on the M3-ID, as shown below:
Here’s a short video showing me placing the flexplate onto the magnetic base, using the rear corner blocks for physical registration.
I’ve already made a number of prints with this system (all the corner blocks – about a dozen by the time I was through) and I have to say it’s like night and day compared to the hassle with my stock M3-ID. If you have a MakerGear M3-ID, this is a must-have!
I created a Thingiverse ‘thing’ with the final designs for the corner block and hold-down clamps.
Stay tuned,
Frank